Exploring Additive Manufacturing with Autodesk Research
Developing new capabilities with industry partners
In the rapidly evolving world of additive manufacturing, Autodesk Research Technical Environments team members Adam Day and Brian Jeong regularly collaborate with industry partners to explore, identify, and experiment with new applications and opportunities in the field. We sat down with them to learn more about their work and discuss Autodesk Research’s unique relationship with Renishaw, a global leader in the field of metrology and additive manufacturing. Through Adam and Brian, we gain a deeper understanding of what it means to interface with the projects and teams using Renishaw’s RenAM 500Q metal additive manufacturing system and discuss the value this machine brings to the innovators shaping the future of additive manufacturing.
Both Adam and Brian have extensive backgrounds in additive manufacturing. Brian, Senior Shop Supervisor at the Autodesk Technology Centre, Toronto, completed master’s studies in additive manufacturing with a focus on laser powder bed fusion and process optimization for Renishaw systems. While attending the research conference Rapid + TCT, Brian learned more about what Autodesk does in the field. “At the time, I wasn’t aware that Autodesk was into additive manufacturing,” Brian says. “But soon after I saw a job posting here in Toronto for a Workshop Specialist role with additive experience – it was great timing.”
Adam’s path to additive came after the Senior Shop Supervisor at the Technology Center in Boston earned a degree in landscape architecture, which led to a role in playground design. Early in his career, a need for 3D printed equipment prototypes required Adam to focus on developing his knowledge in the area. “The 3D printing ecosystem continued to grow enough that now I’m able to focus on just that as my job,” says Adam.
As part of Technical Environments, Adam and Brian help connect the bridge from design to manufacturing for a range of stakeholders. These include Autodesk Research and product teams, Outsight Network residents, industry partners like Renishaw, and external customers. As 3D printing subject matter experts, the two provide advice on how to design and manufacture more effectively. They’re able to help improve workflow processes, resulting in a more fluid experience during the actual manufacturing stage.
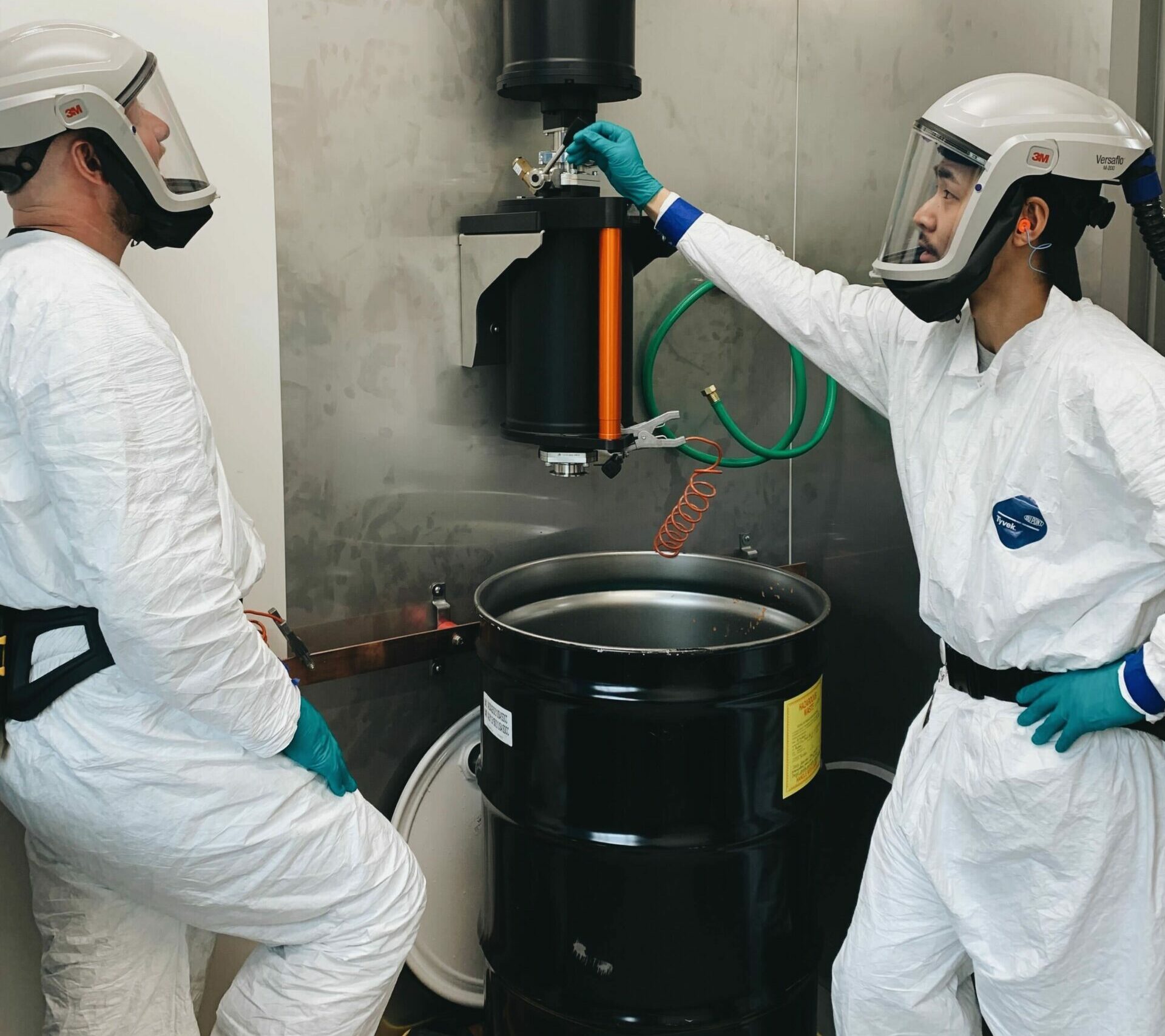
Adam and Brian working with additive materials
Renishaw’s RenAM 500Q 3D printer was commissioned in early 2022 at the Autodesk Technology Center in Boston – the first machine of this type in the city. Referred to simply as “the Renishaw,” this metal 3D printer is one of the most innovative 3D printing systems available. While the machine is printing, it produces and records high-frequency data about the printing process: information like material usage data, melt pool monitoring, and energy consumption. That data is useful for research teams to benchmark against other manufacturing processes, which has huge implications for sustainability efforts. For example, this makes it possible to see if the embodied carbon of manufacturing a 3D printed part is better or worse than CNC machining. How Can Sustainable Manufacturing Save You Money And Help The Planet is a recent study that highlighted the value of these measurements and was presented at AU 2022. That data can also be applied to machine learning or AI systems to improve the process control of printing.
Brian explains: “Autodesk Research teams often come to us for manufacturing and consulting support. So do external customers, machine manufacturers, or other relationships we might have in that area. In the last couple of years, our work with external customers has increased. Machine manufacturers sometimes come to us and say, ’Hey, we’re working with a customer that we would love you to support.’ Or, the request could take the shape of a hybrid project, like Using Fusion 360 and metal AM to optimize automotive mold cooling solutions, a recent automotive manufacturing design and make collaboration between Autodesk and Impression Technologies that was also featured as an AU class this past year. Much of our work focuses on design-to-manufacturing and sometimes manufacturing specifically. If we can do it in-house, then we can help our customers prototype while gathering process data.”
According to Adam: “Another key capability provided by having the Renishaw on site is helping stakeholders to quickly build completely customized parts for projects. If a research project requires a part with specific physical characteristics, like being extremely light and durable but with a high surface area, the Renishaw can make those custom parts for immediate use. It’s really an advantage to have an additive manufacturing machine like the Renishaw in our facilities, enhancing our ability to collaborate with internal teams, particularly around software development. Autodesk can offer unique value because we’ve built out the 3D printing expertise and infrastructure, plus we have the software capabilities that have been tested in-house through the entire workflow.”
Frequent collaboration with product teams allows Autodesk to engage with customers as they transition to this new manufacturing method. Brian agrees: “That’s a great point. Autodesk is really at the forefront when it comes to the manufacturing industry and not only can our software prove it out, but we also have the Technology Centers – physical environments where we’re able to validate a lot of those workflows. For example, we can prepare and send prints directly to the Renishaw from Fusion 360 and work with the Netfabb team on simulation and materials validation. We’re able to showcase this package to customers and share those insights.”
What’s the most impactful part about collaborating with Renishaw for Adam and Brian? Brian values the rare opportunity to be both a technician and engineer of the machine. “Through Autodesk’s relationship with Renishaw, I’m able to get my hands dirty by printing things that have never been manufactured this way before on the machine and working with metal powders,” says Brian. “Autodesk Research is always working on innovative projects, but being able to gain hands-on insight into what our customers are exploring in metal additive manufacturing is fantastic!”
For Adam, it’s about how this machine helps Autodesk engage customers as they transition to this new manufacturing method. He explains: “I think the best part about it is the ability to create parts that can’t be made any other way. There are lots of different geometries that you can only make using metal additive manufacturing and in a lot of cases, laser powder bed fusion. As Brian mentioned, the parts are so rare and it’s such a new technology that being able to make and learn about that process is an incredible opportunity. To be able to lead customers through it and help them solve problems with that technology is so rewarding.”
Get in touch
Have we piqued your interest? Get in touch if you’d like to learn more about Autodesk Research, our projects, people, and potential collaboration opportunities
Contact us